The New Belgium Greenfield site starts up!
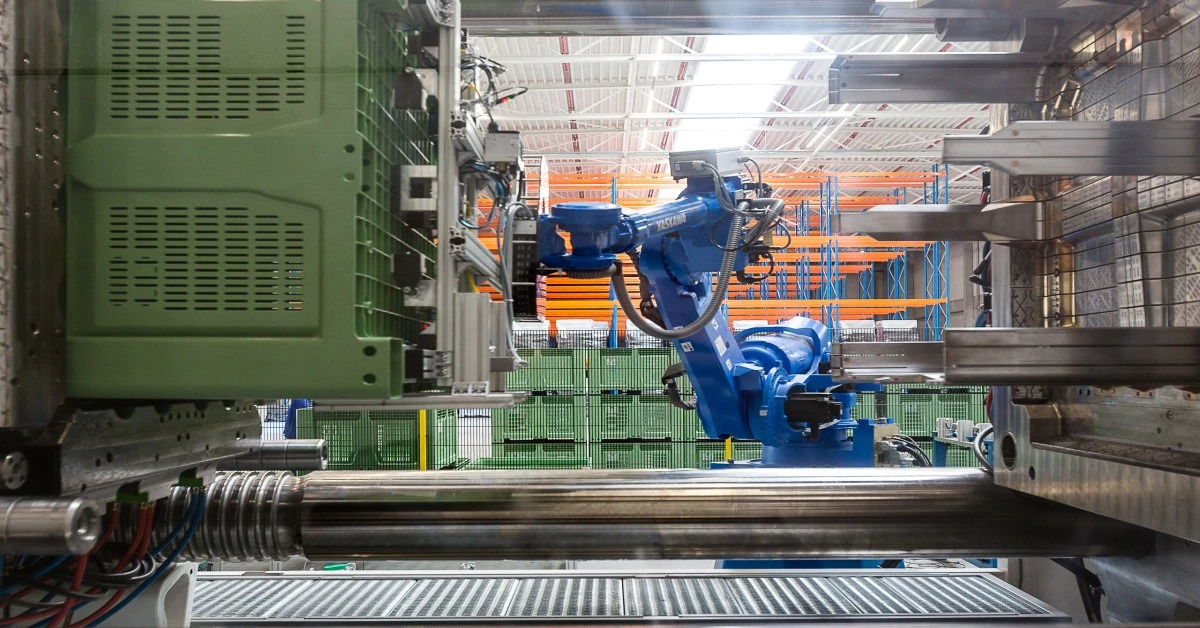
Contact us
Get in touchMaximus®1212 produced at Schoeller Allibert’s new greenfield in Beringen
After months of intensive preparations, Schoeller Allibert’s greenfield in Beringen is finally operational. This light-filled factory, with its state-of-the-art production hall and spacious outdoors storage space, mainly focusses on the larger products in our range. On Friday 18 August, the first Maximus®1212 rolled off the conveyer belt, and on Sunday evening 20 August, the first 1100 pallet boxes left the greenfield to be delivered to the customer.
According to Ludo Gielen, Chief Marketing and Innovation Officer at Schoeller Allibert, it was quite a challenge to install the huge injection moulding machine and the ultra-modern 29 metres long rolling bridge. “This Kraus Maffei is the largest injection moulding machine of the Benelux region. With a closing force of no less than 4000 tons and a shot volume of 60 litres, it produces a Maximus®1212 in two minutes. On 29 August, we already achieved a production of 4500 pallet boxes.”
In order to deliver all pallet boxes in time, the machines are currently working non-stop, 24 hours a day, seven days a week. From the production hall, they head straight to the orchard for the harvest.
Our Maximus®1212 offers numerous advantages over similar plastic pallet boxes on the market. They are lighter and contain up to 35 kg more fruit. And thanks to the unique design, the fruit will receive up to 50% less damage during transportation.
So if you enjoy apples or pears in 2018, they might have been stored in a Beringen Maximus®1212!
Contact us
Get in touchContact us
Inspiration
Related
relevantItems.news.intro
Navigating EU Sustainability Regulations in Transport Packaging—A Roadmap for Compliance and Opportunity
We’re thrilled to introduce our latest whitepaper: New EU sustainability regulations and their impact on packaging. Designed as your essential resource, this whitepaper breaks down the complex, changing landscape of EU s...
Read newsIntroducing SmartLink® by Schoeller Allibert, connecting assets for an intelligent network
Connect and monitor assets with
Read newsSchoeller Allibert's Combo Excelsior® awarded major European Packaging Awards
The Combo Excelsior®, Schoeller Allibert’s new standard foldable intermediate bulk container (IBC) has been awarded the Best Industrial Packaging Prize at the French G.I.S.I. Group’s “Packaging Innovation Awards” and the...
Read news