Innovating waste management: The impact of Renewi and Schoeller Allibert's collaboration
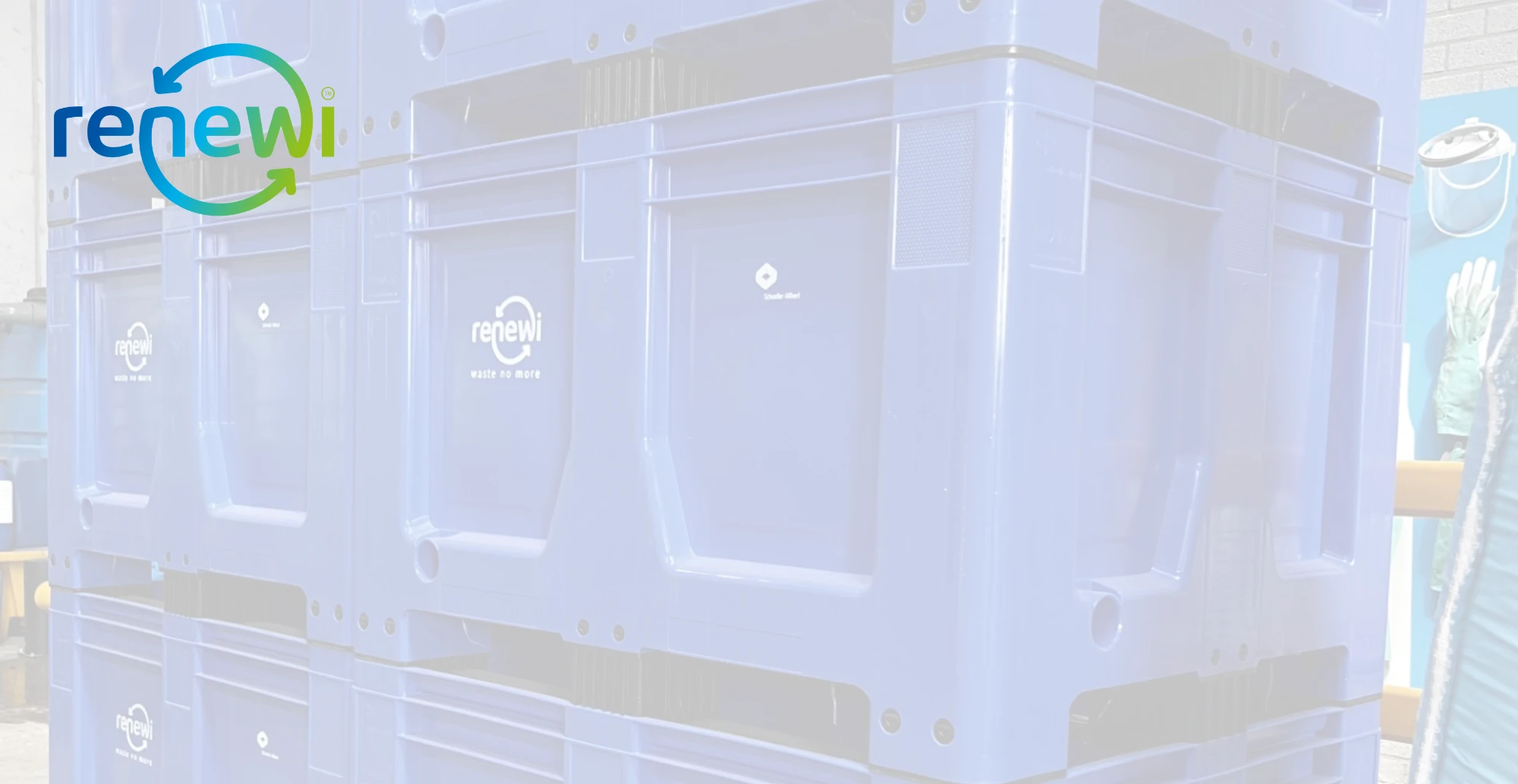
Industry
Contact us
Get in touchRenewi is a leading waste-to-product company dedicated to creating a sustainable future by transforming waste into valuable resources. Operating across 154 operational sites in six countries in Europe, Renewi puts 6.6 million tones of circular materials back into use each year. The company focuses on extracting value from waste rather than incinerating or landfilling it, aligning with both social and regulatory developments.
A partnership built on shared vision
The partnership we developed with Renewi over the years is one to be proud of, as they started primarily as a customer for our MaxiLog® containers. These containers are designed for transporting large volume bulk items. They are strong, sturdy, automation-friendly, safe, and easy to clean. The MaxiLog® is specially adapted to all industrial processing needs, with stackable dimensions making it very efficient for return transport, making it a perfect solution for part of Renewi's waste handling stream.
“At Renewi, we give new life to used materials. Every year we handle almost 11 million tons of waste, of which we recycle 63%, one of the highest in Europe. Including thousands of Schoeller Allibert MaxiLog® containers to collect and move the waste around our facilities."
Jan Pedro Vis, Director Product Management and Innovation at Renewi
Emphasizing sustainability and efficiency
Due to our strong relationship and shared vision on sustainability, our conversations deepened. Renewi faced the challenge of transforming post-consumer waste into valuable resources while enhancing sustainability and efficiency in their operations. Handling 11 million tons of waste annually, with a recycling rate of 63%, Renewi required innovative solutions to further improve their waste collection and transportation processes.
Innovative solutions for a circular economy
We partnered with Renewi to re-introduce the MaxiLog® containers, specifically designed to support a circular economy. Our collaboration focused on utilizing advanced recycling techniques, refining plastic waste, and manufacturing durable, 100% recycled containers to meet Renewi's operational needs.
At Renewi's facilities, a meticulous pre-sorting process was implemented to separate recyclable plastics using vibratory screens, magnets, and sorting cabins. The plastics were then shredded efficiently, allowing for the separation of polyolefins through infrared technology, ensuring purity and eliminating contaminants. The separated plastics were transformed into granules, which were washed, dried, and rigorously tested for quality and purity. These recycled materials were transported to our production facilities, combined with reclaimed plastic from retired MaxiLog® containers.
“We think it’s really important to practice what you preach, so we worked with Schoeller Allibert to form a partnership that is closing the loop. In 2024 we opened a new sorting line for post-consumer plastics. We combine rigid plastics from households with commercial waste, including discarded MaxiLog® containers, to create a high-quality polyethylene, ready to go into new products."
Jan Pedro Vis, Director Product Management and Innovation at Renewi
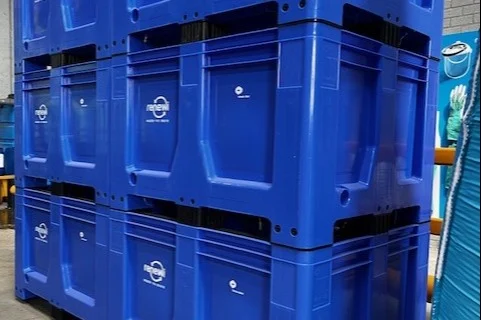
At our manufacturing plant, the recycled materials were fed into specialized molds. Through precision-controlled injection molding, the materials were shaped into robust components, cooled, and adorned with Renewi's logo, ready for deployment. The new containers, crafted from 100% recycled materials, began their journey at Renewi's facilities, housing the next wave of post-consumer waste. After years of intensive reuse, discarded containers would be recycled again to produce new MaxiLog® containers, exemplifying a closed-loop system.
"Plastic itself is not the problem; the issue lies with how we, as consumers, manage and dispose of it. If we can effectively control and manage our plastic waste, we can address plastic pollution. By partnering with Renewi, a leader in waste management, Schoeller Allibert offers solutions for its RTP products that will help mitigate plastic waste pollution."
Carlos de Wever, Manager Materials Innovation at Schoeller Allibert
The environmental and operational benefits
Partnering with Renewi has brought impressive environmental and operational advantages. Our MaxiLog® containers, now made from 98% recycled materials (including 50% old Renewi containers), significantly reduce carbon emissions. Each container saves 82 kg of CO2e compared to those made from virgin materials, slashing emissions by 77%*.
Over a year, using around 3,000 of these boxes prevents 247 tons of CO2e. To put it in perspective, that’s like cutting out the emissions from producing 45,660 steaks, avoiding 20 car trips around the world, or skipping the carbon footprint of nearly 12 million cups of coffee.
*Please note that this is only an estimate which by no means can be interpreted as a representation, warranty or guarantee of any kind. We do not make any (express or implied) representation or warranty as to the accuracy or completeness of such estimate and shall have no liability to you or any other party in relation to the use of such estimate (other than in case of fraud).
“We supply this recycled material to Schoeller Allibert to create a 100% recycled MaxiLog®, used throughout our operations to transport more waste for recycling. Thanks to the high quality of the recycled material, and the excellent design of the MaxiLog®, we know that we have a container that’s ready for high impact activity across our facilities for many years to come. It’s the perfect example of a supply chain partnership promoting the circular economy with long-lived reusable products made with recycled materials.”
Jan Pedro Vis, Director Product Management and Innovation at Renewi
The material innovation in waste management
This project truly is something that comes close to our material strategy and vision, driving our commitment to materials innovation. We are dedicated to researching and developing solutions for hard-to-recycle and hard-to-convert materials, transforming them into durable, high-quality products. Our collaboration with Renewi exemplifies the success of our efforts, proving the viability of recycling and circular economy principles. As future legislation looms, our materials innovation offers promising solutions for waste management. By leveraging advanced technologies, meticulous processes, and a shared vision for sustainability, we contribute to a circular future, one container at a time, demonstrating that no waste is truly waste and driving innovation in waste management.
Are you interested in understanding how we can work together in making your supply chain more circular? Please contact us, and we will reach out to you.
Industry
Contact us
Get in touchContact us
Inspiration
Related
Est proident veniam laborum exercitation est veniam reprehenderit nostrud officia. Ad Lorem aliquip duis labore duis. Irure deserunt eu minim culpa eiusmod quis ut sint eu pariatur magna aliquip et incidid voluptate cillum Lorem amet ea.
Navigating EU Sustainability Regulations in Transport Packaging—A Roadmap for Compliance and Opportunity
We’re thrilled to introduce our latest whitepaper: New EU sustainability regulations and their impact on packaging. Designed as your essential resource, this whitepaper breaks down the complex, changing landscape of EU s...
Read newsCORREOS: postal Services solution in Spain
Discover Schoeller Allibert solution for our Customer CORREOS
Read moreRethink your packaging: Why it’s time to move beyond the Gitter box
The EPAL gitterbox served logistics for decades, but today it slows efficiency, raises costs, and wastes space. Discover why switching to Magnum Optimum® is the smarter, sustainable choice for modern supply chains.
Read news