Customer story: M Leggate & Sons – Fresh RTP solution for UK Brassica Specialist
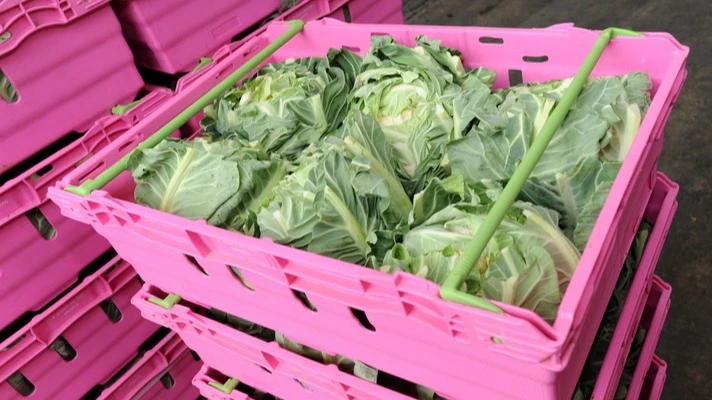
Industry
Contact us
Get in touchTraditionally using wooden crates to transport brassica from field to packing site, or -during winter- from southern Europe growers to their own premises, M Leggate & Sons wanted to move to a more sustainable, safe and hygienic packaging, compliant with BRC standard for use in clean room.
Schoeller Allibert, the UK’s largest manufacturer of plastic reusable transit packaging (RTP), has delivered a fresh idea for leading produce experts, M Leggate & Sons – leading to impressive supply chain cost savings of around €35,000 to date.
Specialists in the growth, preparation and transportation of brassicas (cauliflower, broccoli and cabbages), M Leggate & Sons is committed to providing high quality fresh vegetables to meet the end consumer’s specifications. As certain produce cannot be grown in the UK throughout the year, M Leggate & Sons has built strong relationships with growers across Europe who plant according to their programmes to ensure year round supply to maintain M Leggate & Sons 10 per cent share in the UK brassica market. It is therefore essential that the goods are transported safely and securely using easily distinguishable RTP.
Originally using wooden crates to transport produce, M Leggate & Sons recognised a possible risk of contamination due to the crates being hard to clean, as well as the possibility of contents becoming damaged by splinters or the chemicals used to treat timber against wood borne pests. Additionally, the company required a product that fully complies with BRC standards for use in clean room and could contribute to the company’s policy of zero tolerance on contamination. To resolve these issues, Schoeller Allibert were able to provide sustainable and cost effective alternative in the form of their Maxinest trays, an award-winning range offering a complete field-to-shelf solution for fresh produce. The trays also offer an improved vehicle fill rate on all inbound and outbound trips, contributing to carbon reduction targets which was a key criterion for M Leggate & Sons, saving up to 50 per cent space compared to the previous wooden crates.
Having opted for Schoeller Allibert’s iconic Maxinest tray in bright pink with the company logo printed on the side, M Leggate & Sons also increases in prominence on-shelf while the eyecatching colour helps reduce the risk of stock losses.
Peter Doyle, Schoeller Allibert Sales Manager, says: “The customer came to us through their existing supply chain in mid-2014 expressing their need for new, high-quality RTP. After spending time with the team to fully understand their requirements and suggestions, we were able to recommended a product solution that can offer sustainable growth to the business through greater visibility over the supply chain, reduced storage space and better vehicle fill on return trips for reduced carbon emissions.”
Richard Leggate, of M Leggate & Sons, says: “We found we were increasingly restricted by the wooden crates we were previously using, in terms of both creating a sustainable return supply chain, and product safety and integrity. A change in the equipment we used was imminent, so we began the consultation stage with Schoeller Allibert to discuss the benefits that new RTP could have on our operations. We were able to work closely with the team to choose the product best suited to our market sector and are now reaping the benefits.
Industry
Contact us
Get in touchContact us
Inspiration
Related
Est proident veniam laborum exercitation est veniam reprehenderit nostrud officia. Ad Lorem aliquip duis labore duis. Irure deserunt eu minim culpa eiusmod quis ut sint eu pariatur magna aliquip et incidid voluptate cillum Lorem amet ea.
Navigating EU Sustainability Regulations in Transport Packaging—A Roadmap for Compliance and Opportunity
We’re thrilled to introduce our latest whitepaper: New EU sustainability regulations and their impact on packaging. Designed as your essential resource, this whitepaper breaks down the complex, changing landscape of EU s...
Read newsClient Application: COOPERL Arc Atlantique
Cooperl is one of the top pork meat processing companies in Europe. With 15 slaughtering and processing sites, Cooperl employs 4,800 people and revenue is more than 2 Billion Euros.
Read moreZoom: Egg processing industry - Combo Life
Each European consumer eats about 14,5 kgs of eggs every year. Egg "products" such as liquid egg or egg powder are growing fast due to the heavy trend towards convenience food. Egg processors are delivering to food manuf...
Read more