Schoeller Allibert: The next generation of foldable crates, the future of any sustainable supply chain.
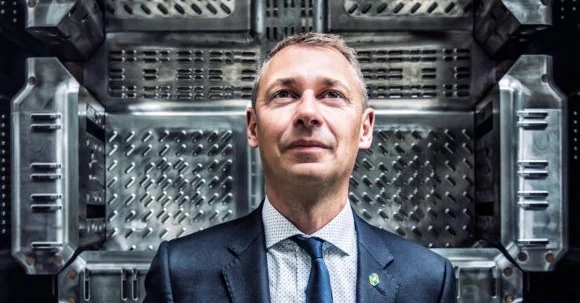
Contact us
Get in touchInterview with Ludo Gielen from Schoeller Allibert about the trends, challenges and solutions for returnable packaging. In Q4 last year, Schoeller Allibert appointed Ludo Gielen as CEO having been with the company since 2004 as Chief Innovation Officer. Under his leadership, many new products have been introduced and “Packaging Revolution” had the chance to discuss with him trends, challenges and solutions, for returnable packaging (RTP) in the years to come.
Inventing and manufacturing reusable crates for the beverage industry since 1960, Schoeller Allibert, the European leader for returnable packaging has one of the strongest R & D teams in the industry and an international manufacturing footprint with a dedicated focus on innovation. In the last 24 months alone, Schoeller Allibert has developed and launched 42 successful new products for eight different end-markets, from new beer crates to foldable large and small containers. Sales of these new products have contributed significantly to revenue growth.
In 1992, Schoeller Allibert founded IFCO (International Food Container Organisation) and remained involved in the business until 2011. Today, the companies continue to work in partnership through an exclusive supply agreement for the third generation “Lift-Lock” container which serves more than 150 million fruit and vegetable customers.
What is next? Obviously, the innovation never stops.
The company won several awards in 2018 recognizing its commitment to innovation, including for the successful launch of fourth generation ‘gold and silver’ beer crates with Warsteiner and for its next generation large foldable container product lines: Excelsior®, Fructus® and Magnum Optimum®. Schoeller Allibert’s engineers are currently focused on the development of the next generation of handheld containers for e-commerce solutions and products such as fruit and vegetables – the 4th generation of foldable small containers.
The new generation will be ultra-flat, helping to save significant logistic costs during empty returns. They will also be lighter, easier to handle and capable of being equipped with smart tracking devices.
Ludo Gielen sees new opportunities to reduce the massive volumes of cardboard that are driving the shift of end users to returnable solutions Ludo also believes digitalisation will disrupt the logistics system and fundamentally change the way returnable crate systems are designed and handled.
In the era of the Internet of Things, with increasing traffic load on our streets, re-thinking is necessary.
Losses are an issue for all pool providers and could be reduced through the implementation of smart crate technologies. Schoeller Allibert is developing rechargeable beacons and creating new features to enable the crates to recharge themselves and provide information on their location. This, combined with new materials and special stacking and nesting profiles, will enable retailers to significantly reduce the space required for stackable folding crates and provide greater insight into their supply chains.
The potential advantages for pooling companies by changing to this new crate are significant and will enable them to be even more competitive for their retailer and grower customers.
The beacons will likely allow the poolers to offer their services without collecting deposits, saving growers and retailers hundreds of millions of Euros. Schoeller Allibert will also provide a recycling service for customers who want to take advantage of this exciting change to the next generation.
Contact us
Get in touchContact us
Inspiration
Related
relevantItems.news.intro
Navigating EU Sustainability Regulations in Transport Packaging—A Roadmap for Compliance and Opportunity
We’re thrilled to introduce our latest whitepaper: New EU sustainability regulations and their impact on packaging. Designed as your essential resource, this whitepaper breaks down the complex, changing landscape of EU s...
Read newsIntroducing JumboNest®, the innovative next generation Rigid Pallet Container (RPC)
Hygienic, fully stackable and designed to maximise freight storage, JumboNest® is the next generation in sustainable, returnable packaging. Food safe, robust and manufactured to withstand extreme temperatures from -7°c t...
Read newsSchoeller Allibert JumboNest® RTP Solution Shortlisted In UK Packaging Awards
Schoeller Allibert, the European market leader in the production of recyclable, reusable and returnable transit packaging (RTP), is celebrating the shortlisting of its newly launched JumboNest® returnable packaging solut...
Read news